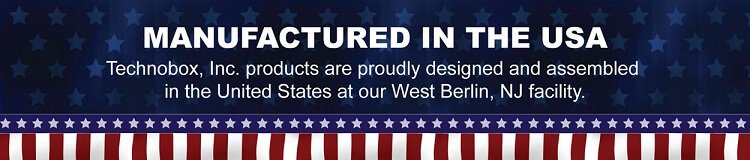
OEM Production Floor & Facility Operation
Technobox, Inc. is a leading supplier of commercial off-the-shelf (COTS) board-level solutions, principally mezzanine card (PMC/XMC) assemblies, as well as associated adapters, carriers and development tools for board deployment and testing. End-user applications address a diverse range of markets including information processing, aerospace/defense, industrial process control and transportation.
Our facility offers a variety of mezzanine board solutions that service supplemental I/O and storage for embedded systems. Designs address a spectrum of possible applications - from a single-width convection-cooled PMC with 4 ports each selectively configured as RS-232, RS-422 or RS-485, to a unique family of XMCs featuring mix-and-match modularity, from which a collection of 4, 8 or 16-port I/O modules can be built and delivered with limited lead times. Our extensive product offerings facilitate the engineering and/or testing of XMC and PMC mezzanine boards or to enable their integration within a variety of system platforms such as OpenVPX, VME and standard PCI Express (PCIe). In addition to our mezzanine solutions, Technobox, Inc. offers a variety of accessories that further add to product performance and capabilities including transition panels, extenders and cables.
Every aspect of production happens in-house. Our machining area comes equip with a NC X/Y milling/drilling table, a Fusion 3 3D printer, drill press, vice and numerous other devices for making modifications to standard products, as well as producing fixtures as needed by the manufacturing line. All boards and accessories manufactured by Technobox, Inc. undergo extensive functionally testing by highly-qualified production specialists and engineers. Designed, assembled, delivered – you request and we respond!
Our shipping area contains various storage bins for both small quantity items and higher volume products. We keep several boards of each P/N on hand for small quantity sales as well as servicing warranty spares. The centrally located shipping table, with ESD protective mat, is where products are staged daily for shipment using pink ESD peanuts and corrugated cardboard boxes.
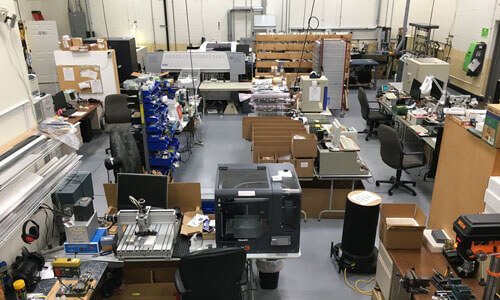
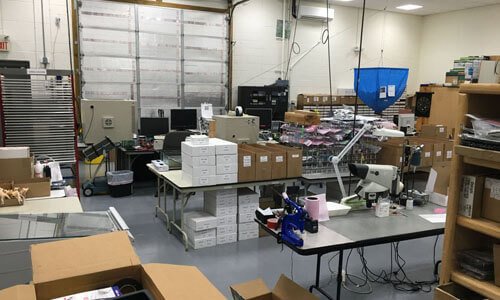
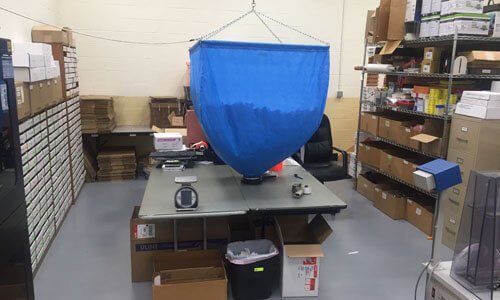
Primary Surface Mount Technology (SMT) Line
Our extensive SMT line houses top-of-the-line manufacturing equipment starting with our RD2 Vapor Phase reflow oven. Technobox, Inc. uses Galden LS230, which has a precise boiling point of 230 deg C. The reflow process works for tin/lead soldering for older products (c. 1997 to 2005). Future designs and manufacturing will be RoHS.
Next is our SpeedPrint 700 stencil printer. This machine is manually loaded and unloaded with boards and has 2D paste inspection capability used for fine pitch components. Its under-stencil wipe typically operates every 2-to-10 prints depending on the board complexity. Further on is our MEK Automatic Optical Inspection (AOI) station. With design complexity, inspection by an operator under a microscope becomes impractical, but the MEK AOI automates the process and shows the operator suspicious solder joints and improperly mounted components – rejected boards are fixed and retested.
Unlike the “dishwasher” style of most SMT lines, our X30A washing machine has a chemical wash followed by a closed loop deionized water rinse. The wash and rinse fluids impinge on the boards in a broadside manner, thereby getting under low profile components to wash away flux residues. Our process is Water Soluble Flux (compared to no clean flux) since properly washing the boards is critical, flux residue is left, which is very compatible with conformal coat processing. Conformal coating is handled by an external supplier.
The MyData (MY100LXe) pick-and-place machine is the heart of our SMT line. It is equipped with a manual load adapter for securing the boards during manufacture, a “tray wagon” for matrix supplied components and several “magazines” for handling components in a variety of packaging. The machine features a high-resolution camera for managing fine pitch components, as well as the electrical test option for validating component reels when a new reel is loaded on the machine. Perfect for high mix, high complexity, low volume manufacturing of printed circuit assemblies.
Our DryBoxes hold tube and matrix tray inventory and are moisture-sensitive components that need maintenance in a dry environment (our RH is typically 4% in the DryBox) to avoid popcorning of components from steam buildup in the component package. DryBoxes are also used for staging production runs, since we condition our bare printed circuit boards with a 4 hour, 110 deg C bake to remove any moisture.
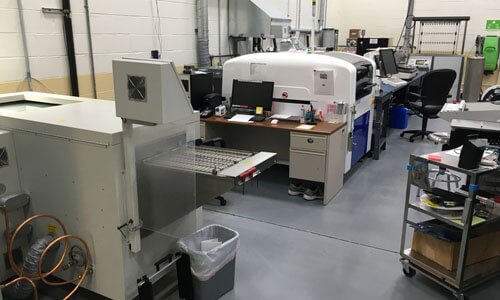

